Introduction
On March 26, 1993, a catastrophic explosion shook Baytown, Texas, registering 4.3 on the Richter scale. This event not only left a profound mark on the local community but also raised significant questions about industrial safety and disaster preparedness in one of America’s key industrial hubs.
Background of the Area
Baytown, located east of Houston, is part of the Gulf Coast petrochemical complex, a critical region for the oil and gas industry. Home to several refineries and chemical plants, including the prominent Amoco Chemical Company facility, Baytown’s economy heavily relies on the petrochemical sector. The concentration of hazardous materials and industrial operations made the city particularly vulnerable to accidents.
The Incident
The explosion occurred at approximately 10:30 a.m. at the Amoco Chemical Company plant. A combination of mechanical failure and procedural lapses led to the release of a large volume of flammable gases. Eyewitness accounts describe a blinding flash followed by a powerful shockwave, with reports of the ground shaking as far as five miles away. The explosion was so intense that it caused structural damage to nearby buildings and shattered windows in homes and businesses throughout the surrounding area.
Emergency responders rushed to the scene, battling fires that erupted from the blast. The initial chaos was compounded by the uncertainty surrounding the potential for additional explosions or hazardous chemical releases.
Casualties and Damage
The explosion claimed the lives of several workers at the plant and resulted in numerous injuries among both plant personnel and nearby residents. In total, more than 100 individuals required medical attention for injuries ranging from burns to respiratory issues due to exposure to chemicals.
In terms of physical damage, the explosion devastated the immediate area, damaging over 100 structures. Homes, schools, and businesses were affected, leading to significant property loss. The economic impact extended beyond immediate repairs, as businesses faced disruptions and residents grappled with the emotional toll of the disaster.
Response and Investigation
In the aftermath, federal and state authorities, including the U.S. Chemical Safety and Hazard Investigation Board (CSB), launched an extensive investigation to determine the explosion’s cause. Their findings revealed critical lapses in safety protocols, including inadequate maintenance practices, failure to adhere to safety regulations, and insufficient employee training regarding the handling of hazardous materials.
The investigation also highlighted communication failures within the plant, where safety alarms and alerts were either malfunctioning or ignored. These findings prompted calls for greater oversight and regulation of chemical manufacturing practices.
Legislative and Regulatory Changes
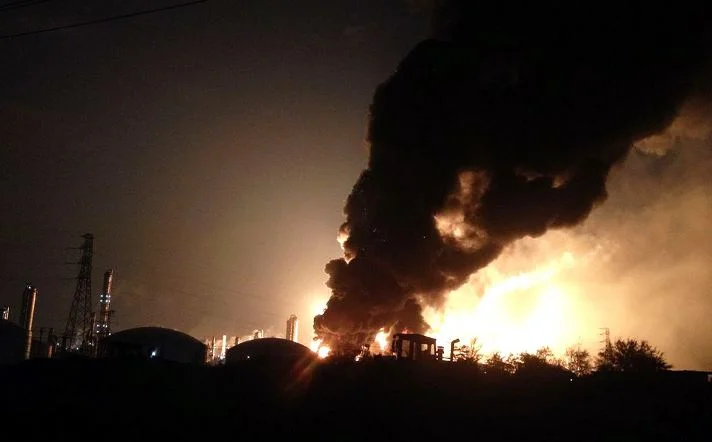
The Baytown explosion led to increased scrutiny of safety protocols across the chemical industry. In the years following the incident, the Occupational Safety and Health Administration (OSHA) and the Environmental Protection Agency (EPA) enhanced regulations to improve workplace safety and chemical handling practices. New legislation aimed at improving emergency response preparedness and ensuring more stringent inspections of chemical facilities was introduced.
Additionally, companies began to invest more in safety technology, including advanced monitoring systems that could detect gas leaks and alert personnel before an incident escalated.
Community Impact
The explosion profoundly impacted the Baytown community. Beyond the immediate physical destruction, it left an emotional scar on residents who witnessed the event or lost loved ones. Community organizations rallied to support victims and their families, offering counseling services and financial assistance for those displaced by the explosion.
In the years following the disaster, Baytown focused on rebuilding and recovery. The city implemented community programs aimed at enhancing disaster preparedness, encouraging residents to participate in training sessions on emergency response and evacuation procedures. Local schools also integrated safety education into their curricula, emphasizing the importance of awareness regarding industrial hazards.
Economic and Environmental Considerations
Economically, the explosion posed challenges as businesses faced interruptions and repairs. However, it also sparked discussions about the future of industrial operations in Baytown. Many community members began advocating for a balance between economic development and environmental safety, urging policymakers to consider the long-term impacts of industrial activities on health and the environment.
Environmental assessments conducted post-explosion monitored air and water quality in the area. While immediate hazards were managed, ongoing vigilance was necessary to ensure the health of both residents and the local ecosystem.
Case Study: The Baytown Explosion of 1993
Overview
On March 26, 1993, the Amoco Chemical Company plant in Baytown, Texas, experienced a catastrophic explosion that registered 4.3 on the Richter scale. This incident resulted in several fatalities, numerous injuries, and significant damage to surrounding properties. It raised serious concerns regarding industrial safety and emergency preparedness.
Key Findings
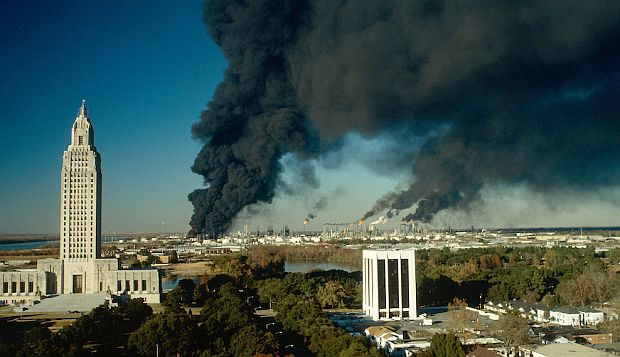
Cause of the Explosion: A combination of mechanical failures and procedural lapses led to the release of flammable gases, which ignited.
Impact: The explosion caused the death of several plant workers, injured over 100 individuals, and damaged more than 100 buildings in the vicinity.
Response: Emergency services worked quickly to contain fires and manage the aftermath, while federal and state agencies initiated an investigation.
Regulatory Changes: The incident prompted revisions to safety protocols and regulations within the chemical industry, leading to enhanced safety measures and training.
Community Recovery: The explosion left a lasting impact on the Baytown community, prompting initiatives focused on disaster preparedness and emotional support for affected residents.
Lessons Learned
Importance of Safety Protocols: Stringent safety measures and regular maintenance are essential in preventing industrial accidents.
Emergency Preparedness: Communities should develop robust emergency response plans to effectively manage industrial hazards.
Regulatory Oversight: Stronger regulations and inspections can help mitigate risks associated with hazardous materials.
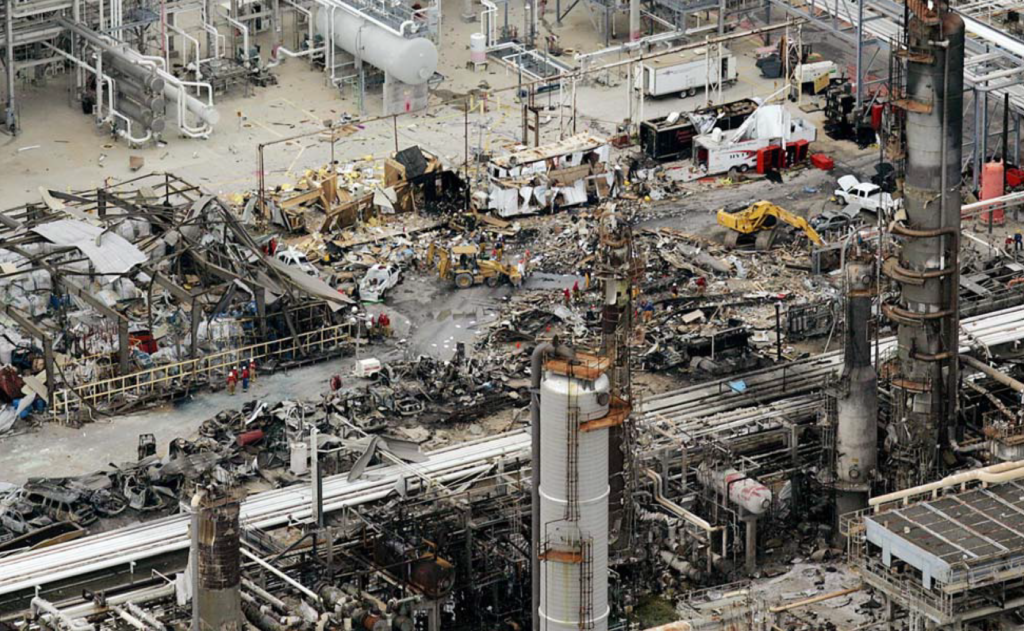
FAQ
1. What caused the Baytown explosion?
The explosion was caused by a combination of mechanical failures and procedural lapses at the Amoco Chemical Company plant, leading to the release of flammable gases.
2. How many people were affected by the explosion?
Several workers lost their lives, and more than 100 individuals were injured, including both plant employees and nearby residents.
3. What measures were taken after the explosion?
An investigation was launched, leading to regulatory changes aimed at improving safety protocols in the chemical industry. The community also focused on recovery and disaster preparedness initiatives.
4. How did the explosion impact the local community?
The explosion caused significant physical damage and emotional distress among residents, prompting community support efforts and changes in local safety education.
5. What lessons were learned from the Baytown explosion?
The incident underscored the importance of stringent safety measures, emergency preparedness, and the need for regulatory oversight in industrial operations.
Conclusion
The Baytown Explosion 1993 4.3 Richter Scale remains a significant chapter in the history of industrial safety in the United States. It serves as a stark reminder of the potential dangers associated with chemical manufacturing and the critical need for stringent safety measures. As the community continues to heal and grow, the lessons learned from this tragedy underscore the importance of vigilance in protecting both workers and residents from industrial hazards, paving the way for a safer industrial future.