Introduction
The ACTT Service Program SP 3-872-009 Shut Down Harness is a vital safety component used in various industrial and automotive settings. Its primary role is to ensure quick and reliable power disconnection in emergencies, thereby protecting both personnel and equipment. This article will provide an in-depth look at the harness’s purpose, design, installation, and maintenance, ensuring clarity and ease of understanding.
Purpose of the Shut Down Harness
The Shut Down Harness is designed to enable rapid disconnection of power from machinery or equipment during emergencies. This functionality is crucial for:
Preventing Accidents: Quickly cutting power can avert potentially dangerous situations.
Minimizing Damage: Immediate disconnection helps protect machinery from further damage during a fault.
Enhancing Safety: The harness serves as a critical safety feature for operators and workers.
Key Design Features
Material Composition
The harness is typically made from durable materials that can withstand harsh operational environments. Key materials include:
High-Temperature Insulation: Protects against heat damage.
Robust Connectors: Built to resist corrosion and wear.
Flexible Wiring: Facilitates easy installation and adaptability.
Electrical Specifications
The Shut Down Harness is designed to accommodate specific voltage and current ratings. Adhering to these specifications is essential for safe and efficient operation.
Safety Mechanisms
Modern versions of the harness often include several safety features:
Quick-Disconnect Connectors: Allow for fast power disconnection.
Status Indicator Lights: Provide visual feedback on power status.
Fail-Safe Functions: Automatically cut power in the event of a fault.
Installation Steps
Installing the Shut Down Harness correctly is essential for its performance. Here’s a step-by-step guide:
Preparation
Consult the Manual: Read the manufacturer’s instructions thoroughly.
Gather Necessary Tools: Tools like wire strippers, crimping tools, and screwdrivers are typically required.
Identify Connection Points
Locate where the harness will connect to the power source and the equipment. This involves:
Disconnecting Power: Always ensure the power is turned off for safety.
Mapping the Circuit: Understand the circuit layout to ensure proper connections.
Making Connections
Strip Wires: Use wire strippers to expose the ends of the wires.
Crimp Connectors: Securely attach connectors to the harness wires.
Connect to Power Source: Link the harness to the appropriate terminals on both the power source and equipment.
Testing the Installation
After installation, it’s critical to test the harness:
Power On: Restore power and check for proper operation.
Conduct Emergency Test: Simulate an emergency to ensure the harness functions correctly.
Maintenance and Troubleshooting
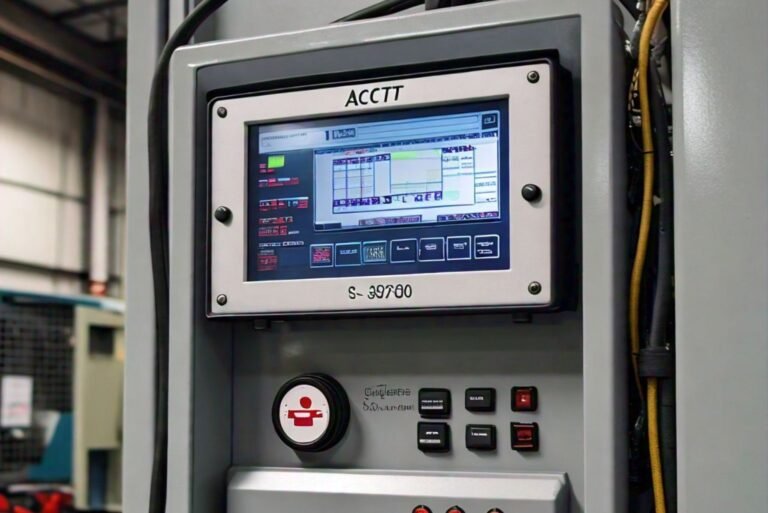
To ensure long-term reliability, regular maintenance of the Shut Down Harness is essential. Here are some key practices:
Routine Inspections
Conduct regular checks for:
Wear and Tear: Look for damage or corrosion on connectors and wiring.
Connection Security: Ensure all connections are tight and clean.
Cleaning
Keep the harness free of dust, oil, and other contaminants. Use non-damaging cleaning agents suitable for electrical components.
Functionality Testing
Periodically test the harness, especially after any maintenance work, to confirm it operates as intended.
Troubleshooting Issues
If problems occur:
Check Connections: Make sure all connections are secure.
Inspect for Damage: Look for visible signs of wear.
Consult Documentation: Use the manufacturer’s troubleshooting guide for specific issues.
Case Study: Implementing the ACTT Service Program SP 3-872-009 Shut Down Harness
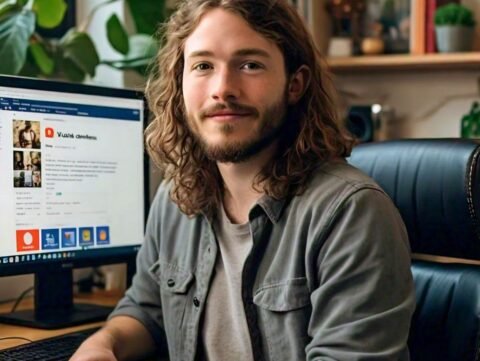
Background
In a manufacturing facility producing automotive parts, the safety of machinery and personnel is paramount. The facility identified the need for a reliable safety mechanism to ensure quick power disconnection during emergencies. The ACTT Service Program SP 3-872-009 Shut Down Harness was chosen for its proven reliability and robust safety features.
Implementation
Step 1: Needs Assessment The safety team evaluated existing safety protocols and identified potential hazards in the machinery operation process. The decision was made to integrate the Shut Down Harness into critical machines, such as CNC mills and presses.
Step 2: Installation Qualified technicians followed the manufacturer’s guidelines for installation. They ensured proper connections and conducted initial testing to confirm functionality. The harness was integrated with existing emergency stop systems.
Step 3: Training All operators received training on the new system, focusing on how to use the Shut Down Harness effectively. Emergency drills were conducted to familiarize staff with rapid disconnection procedures.
Step 4: Monitoring and Maintenance Regular inspections were scheduled to monitor the condition of the harness. Any signs of wear were addressed promptly, and functionality tests were conducted quarterly.
Results
Within three months of implementation, the facility reported a significant reduction in safety incidents. Operators felt more secure knowing that they could quickly disconnect power during emergencies, leading to increased productivity and morale.
FAQ: ACTT Service Program SP 3-872-009 Shut Down Harness
1. What is the ACTT Service Program SP 3-872-009 Shut Down Harness?
The Shut Down Harness is a safety device designed to quickly disconnect power from machinery in emergency situations, enhancing operator safety and equipment protection.
2. How does the Shut Down Harness work?
It functions through quick-disconnect connectors that enable rapid disconnection of power, often integrated with existing emergency stop systems.
3. What materials are used in the harness?
The harness is made from high-temperature resistant insulation, durable connectors, and flexible wiring, ensuring reliability in various environments.
4. How do I install the Shut Down Harness?
Installation involves disconnecting power, mapping connection points, attaching connectors securely, and testing functionality. Always follow the manufacturer’s instructions.
5. What maintenance is required for the harness?
Regular inspections for wear and tear, cleaning to remove contaminants, and functionality testing are essential for maintaining the harness.
6. Can the harness be used in different types of machinery?
Yes, the Shut Down Harness is versatile and can be used in various industrial and automotive applications, as long as it meets the electrical specifications of the equipment.
7. What should I do if the harness fails during operation?
If the harness fails, immediately follow emergency protocols to disconnect power manually if safe to do so. Consult the manufacturer’s troubleshooting guide and have qualified personnel inspect the harness.
8. Are there any certifications or standards that the Shut Down Harness complies with?
Yes, the Shut Down Harness typically meets various industry safety standards and certifications. It’s essential to check the product specifications for compliance details relevant to your industry.
Conclusion
The ACTT Service Program SP 3-872-009 Shut Down Harness is an essential safety device in various industrial and automotive applications. Understanding its purpose, design, installation process, and maintenance is crucial for ensuring both safety and operational efficiency. By following the guidelines outlined in this article, operators can effectively use the harness, reducing risks and enhancing safety protocols in their work environments.